GAIM Inyeccion asistida con gas
Procesos > ► Inyección
¿Qué es el moldeo por inyección asistido por gas?
Una forma práctica de ofrecer flexibilidad en el diseño: una forma inteligente de reducir costes. El moldeo por inyección asistido por gas (GAIM) es un proceso de moldeo por inyección mejorado que a menudo se aplica para piezas complejas, piezas grandes y piezas que requieren un acabado cosmético atractivo. Los tipos de piezas que más se benefician de este proceso incluyen:
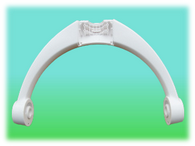
- paneles grandes
- recintos
- manejas
- puertas y biseles
- piezas en forma de tubo o varilla
¿Cómo funciona la asistencia de gas?
El proceso asistido por gas se introduce al final de la etapa de llenado del molde mientras la resina aún es líquida. Se usa gas presurizado (generalmente nitrógeno) en lugar de la presión del paquete de la máquina de moldeo. La presión del gas completa el llenado de la cavidad del molde, forzando una distribución uniforme de la resina fundida contra el molde. El gas se mantiene en el interior durante toda la fase de enfriamiento y luego se ventila, dejando un vacío. Para el moldeo interno asistido por gas, el vacío está dentro del plástico. Para el moldeo asistido por gas externo, el hueco está en la superficie exterior, típicamente en la parte trasera de una pieza.
Beneficios
El proceso asistido por gas obtiene resultados cuando los elementos de diseño de la pieza dificultan la fabricación de la pieza mediante moldeo por inyección recta. GAIM permite una mayor flexibilidad de diseño sin dejar de ofrecer estos beneficios:
- Piezas de paredes delgadas con mayor resistencia y rigidez
- Creación de áreas ahuecadas, reduciendo el peso de la pieza.
- Reducción de la tensión moldeada para mejorar la estabilidad dimensional
- Mejor acabado superficial sin marcas de hundimiento
- Menor contracción de la pieza y menor deformación
Ventajas de diseño con asistencia de gas
1. Diseños complejos
Para el ingeniero de diseño, el uso de GAIM amplía las opciones de diseño y ayuda a minimizar los cambios de diseño para que la pieza se pueda fabricar mediante moldeo por inyección. Uno de los mayores beneficios es la capacidad de producir piezas complejas. A menudo, con el moldeo por inyección recto, las piezas que tienen diferentes espesores de pared se moldean por separado y se ensamblan posteriormente. GAIM permite combinar varias piezas en una, lo que reduce la necesidad de procesos de ensamblaje secundarios, incluso si las piezas tienen diferentes espesores de pared. Esto se debe a que la asistencia por gas permite que las secciones de paredes pesadas se crucen con las más delgadas. Las nervaduras de soporte y las protuberancias pueden lograr tolerancias más estrictas y diseñarse más grandes sin temor a marcas de hundimiento. Los canales de gas se dirigen hacia estas áreas y la presión constante durante la fase de enfriamiento elimina las marcas de hundimiento, asociadas con estas características de soporte, en la parte frontal de la pieza.
2. Reemplazo de metales
La asistencia por gas permite la producción de componentes de paredes delgadas que tienen áreas sólidas pero huecas. La resistencia resultante y la pieza liviana a menudo pueden reemplazar las piezas fabricadas en metal o fundidas a presión y reducir el costo del producto.
3. Piezas grandes
La introducción de presión de gas ayuda en el llenado del molde, proporcionando una presión uniforme en toda la pieza que dura a través de la etapa de enfriamiento. El resultado es una pieza con menos encogimiento y deformación reducida. El peso de la pieza también se puede reducir creando áreas ahuecadas.
4. Acabados cosméticos
Cuando se requiere una superficie con un acabado atractivo, la asistencia de gas evita las áreas de hundimiento, lo que elimina o al menos minimiza las operaciones secundarias para mejorar la apariencia de la pieza, incluido el lijado y la imprimación.
5. Partes huecas
El gas puede crear áreas ahuecadas dentro de piezas como manijas, lo que reduce el peso de la pieza y aún proporciona resistencia.
Beneficios de costos con Gas Assist
1. Mayor vida útil de la herramienta
Con la asistencia por gas, se requiere una fuerza de sujeción más baja porque se utilizan presiones más bajas. Esto da como resultado un menor desgaste del molde, lo que prolonga la vida útil de la herramienta.
2. Menor costo de energía
Con una fuerza de sujeción menor requerida, se pueden utilizar moldes más grandes en prensas más pequeñas. Las prensas más pequeñas consumen menos energía y ayudan a reducir el costo de fabricación de la pieza.
3. Menos tiempo de máquina
Un período de enfriamiento más rápido ayuda a reducir el tiempo del ciclo, lo que a su vez reduce los gastos de fabricación por pieza.
4. Menor costo de material
Se utiliza menos material para producir la pieza porque las áreas huecas dentro de la pieza se crean con el gas y con menos resina utilizada, el costo de la pieza se reduce.
5. Resultados de calidad
Con el moldeo por inyección asistido por gas, el proceso suele ser más fácil de controlar que el moldeo por inyección convencional . Un proceso confiable y repetible proporciona resultados de producción consistentes y menos desperdicio.
Diseño de herramientas de asistencia de gas
Si desea obtener resultados de alta calidad, asegúrese de obtener el diseño de herramienta correcto. Independientemente del proceso de moldeo por inyección que se utilice, es importante involucrar a su moldeador durante las primeras etapas del diseño de la pieza en la fase de diseño para fabricación (DFM). El costo de la herramienta, el cronograma y la calidad de la pieza resultante se verán directamente afectados por la calidad y eficacia de la herramienta. Al determinar la forma óptima de moldear una pieza, los ingenieros considerarán todos los requisitos del producto, incluida la aplicación, la selección de resina y las consideraciones de costo. El análisis de flujo del molde se utiliza para encontrar restricciones de diseño de modo que se puedan realizar ajustes. Cuando el ingeniero de herramientas determina que la asistencia por gas es la mejor solución, la herramienta se diseñará con canales de gas integrados en el molde que permitirán la adición de gas nitrógeno durante el proceso de moldeo. Determinar su método de moldeo temprano conservará el costo de las herramientas y ayudará a mantener los plazos del proyecto
Libertad de diseño
- Integración funcional de múltiples piezas de plástico en un solo conjunto
- Posibilidad de combinar secciones de paredes gruesas y delgadas en la misma pieza
- Rigidez mejorada utilizando secciones huecas de "viga de caja"
- Calidad de pieza mejorada
- Reducción de la deformación y la distorsión debido a una menor contracción diferencial
- Eliminación de marcas de hundimiento
- Menos marcas de flujo y líneas de soldadura debido a la necesidad de menos puntos de inyección
- Costos de fabricación reducidos
- Menor peso total de la pieza terminada debido a las secciones de pared reducidas
- Tiempos de ciclo más cortos debido a secciones de pared más pequeñas y tiempos de enfriamiento más cortos
- Menores costos de energía debido a la menor fuerza de sujeción del molde y al empaque de plástico
- Costos de ensamblaje reducidos debido a la integración de piezas
- Costos de inversión más bajos
- Fuerza de sujeción del molde más pequeña debido a presiones de inyección más bajas y, por lo tanto, máquinas de moldeo por inyección más pequeñas
- Costos de herramientas reducidos debido a presiones de inyección más bajas
- Menores costos de mantenimiento debido al menor desgaste de los moldes debido a menores presiones de inyección
Aplicaciónes
El proceso se utiliza en una amplia gama de sectores del mercado, incluidos el automóvil, la televisión, la informática, la telefonía móvil y los electrodomésticos porque le da al diseñador de componentes una mayor libertad, al moldeador menores costos de inversión y más control sobre la calidad de la pieza terminada y, lo que es más importante, proporciona al usuario final importantes ahorros de costes.